Could this 3D-printing startup remove one of the biggest construction costs in Dubai?
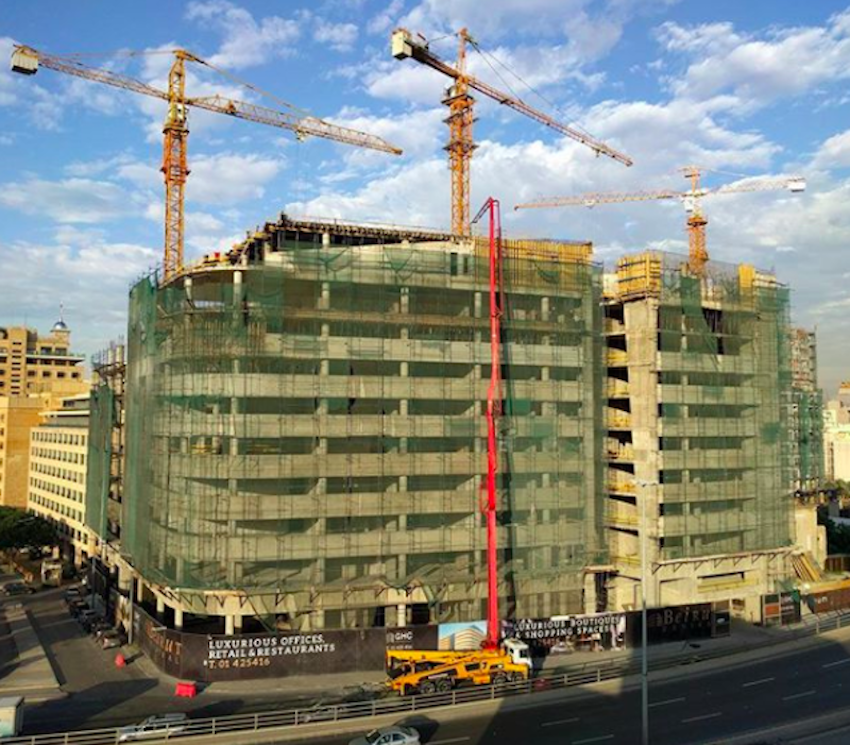
I met two startups in less than two weeks working in innovating the construction industry. And this is only in Lebanon.
One cannot deny, this sector has been in the comfort zone [away from tech disruption] for quite a while now but things are swiftly changing and more innovative solutions are making the construction more efficient, less expensive, and greener.
With the Expo 2020 in Dubai just around the corner, the supply for building properties is increasing and fears of an explosion in supply over demand is rising. Hussain Sajwani, chairman of DAMAC Properties, one of the real estate companies in the UAE, couldn’t disagree more.
In a television interview with Bloomberg, he assured that the supply does not exceed demand. In Dubai, they require to build 18,000 to 22,000 of units, but they have supplied so far around 12,000. “So we don’t have too much over supply coming in. We have seen some softening in the prices in the last couple of years. Now, it’s stable,” said Sajwani in the interview.
However, regardless of whether the country is witnessing an explosion in supply or not, one thing remains constant: Construction startups are perceiving Dubai as their revenue haven.
“I won't be surprised if the real estate sector becomes a net energy contributor in the next decade rather than a consumer,” said Omar Chihane, the CEO of SellAnyHome, an online marketplace to sell and buy properties. “I think the real estate sector anywhere in the world is on the verge of changing for the better. VC money had been pouring into this sector at an astonishing rate since 2010. 150 times more money invested in property tech since 2010. We believe the more transparent and faster a transaction becomes the more valuable the sector becomes as it encourages new entrants and that's what we are trying to tackle.”
A previous interview we did at Wamda was with a startup called WakeCap, which is developing a smart device that gets installed on construction helmets, to transmit data about workers’ activities and their environment. This technology will help engineers and contractors identify problems on-site quickly, pick up any extreme weather condition on-site, manage workers’ activities and other tasks. The data will help in improving decision-making on-site. The startup is also planning on selling the device to a helmet manufacturing company in Dubai, and to raise funds from a VC in the Emirate, to help them scale faster into the market. The team is currently testing their product in Lebanon.
That’s the first startup. The other one, also starting out from Lebanon and targeting Dubai, is Buildink. It focuses on the green aspect of construction.
3D-printed buildings are coming faster than you think
Developed by a team of seven - CEO Bilal Farshukh, CTO Moalla Ilani, material engineer Khaled Bukhari, robotics engineer Jad Itani, electronics engineer Mohamed Bakri, software engineer Mohyddin Tash, and software consultant Fouad Balhawan - Buildink is a 3D printer that produces cement blocks used in construction buildings.
The cement, which mix remained undisclosed and scribed as a ‘secret ingredient’, is supposed to be three times stronger than regular cement mixes. It has a setting time 30 times faster, flows better in the printer, and transmits less carbon dioxide, said Farshukh in an interview with Wamda. The team ran several testing with engineering company ACTS, on different 3D printers, to check the quality of the cement and how big the printer should be to produce more blocks, faster.
The first test was done on a 1x1x1 meter cubical frame using the 3D printer, as shown below.
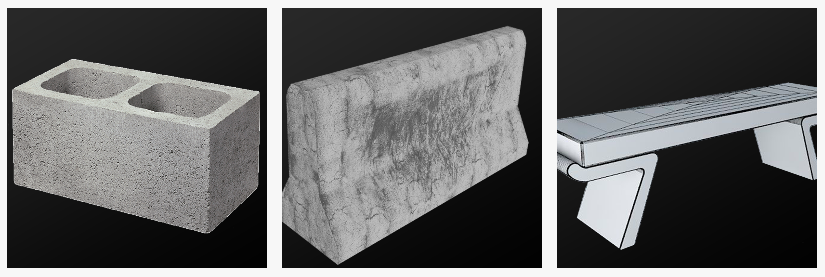
The test was successful, but the frame needed to be bigger to save cost and increase quantity. So they developed another printer which is made of cable ropes and pulleys. They bought the printer parts from China and assembled them at the UK Tech Hub in Lebanon.
The second prototype was a 2x2x2 m frame, but the investors they have been talking to want the team to scale that to 10x5x5 m frame, which will allow Buildink to print an entire level, according to the CEO. The reason why this solution might be attractive to investors - despite the fact that the cement mix is more expensive - is because the process requires only one worker to operate the 3D printer, so the construction company would still be saving more money and getting faster output, said software engineer Tash.
“The mix we are using is 20 percent more expensive than the usual one. On a large scale, when we start bringing bigger quantities, the number will change. If we are printing a 2x2x2 m block, with the regular mix this would cost us 100,000 Lebanese pounds (around $67), now [with the Buildink mix] it’s costing us around $100,” explained Farshukh. “But our plan is to print single-storey houses quicker and we won’t have a lot of workers on-site so we’re saving on cost and time. It would still be profitable to have our mix a bit more expensive.”
As for the reason why they are targeting Dubai, Farshukh added that the Emirate wants to have 25 percent of their buildings 3D-printed by 2030, and one of the investors they are talking to - which remained anonymous - works in 3D printing in Dubai and might be able to help them access the big market players.
Dubai’s first 3D-printed building was announced in 2016, yet it was only assembled in Dubai and printed in China, according to Farshukh.
Buildink is focusing on 3D-printing single storeys for the time being, but will be moving to bigger constructions later on. Here's a video of how their 3D printer works: